Latest News & Events
Explore innovative solutions for sheet metal processing and sheet metal processing types and applications
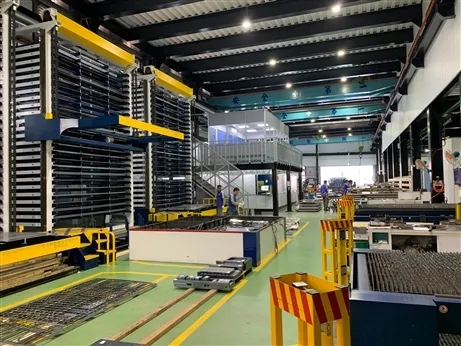
The bending process is a crucial process in sheet metal machining. It is the process of producing plastic deformation of metal sheets through additional forces. The key is to give the cutting part curvature along the axis. The process of applying external forces to the mold, in addition to the need to take into account the shape of the mold, including the bending radius (R angle) and the rebound factor, affect the results of the mold.
The angle part is affected by the rebound factor, and it is often difficult for the first bend to reach the expected angle, so many bending devices now have a compensation mechanism for angle detection, which allows you to correct the angle secondarily. In addition, the size of the workpiece (known in the industry as the outside size or the size in the bag) is influenced by the material properties (K-factor), which is largely dependent on the experience of the factory's professional technicians. In addition to decades of bending processing experience, Steel Metal has also been actively introducing bending software and automatic tool changing systems in recent years to meet the increasingly complex bending needs.
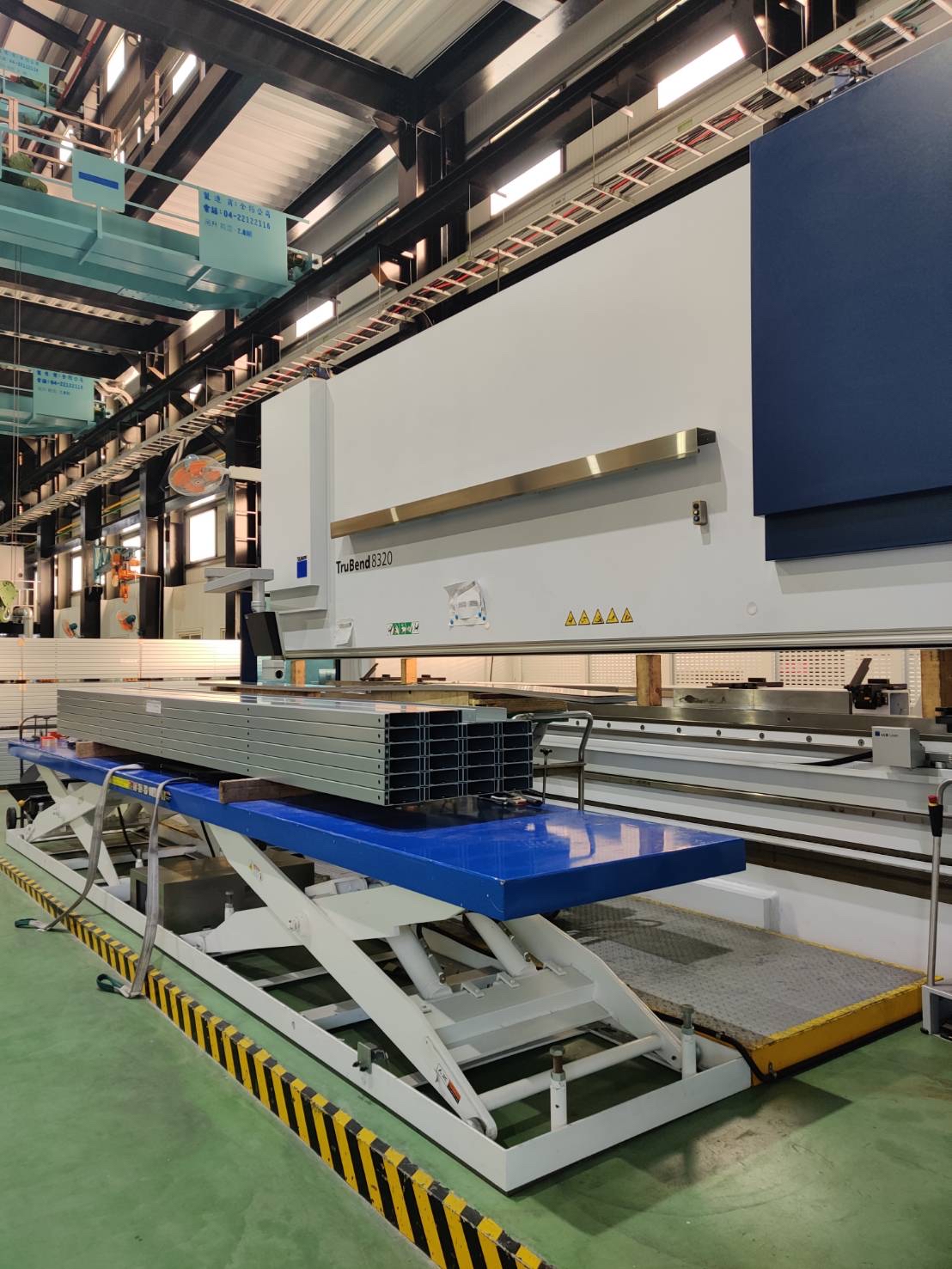
Bending Equipment
TRADITIONAL HYDRAULIC CRIMPING MACHINE, DRIVEN BY HYDRAULIC CYLINDER, PROVIDES STABLE PRESSURE (20-200 TONS), SUITABLE FOR BENDING OF VARIOUS TYPES OF PLATES. However, in recent years, international manufacturers have launched servo-driven folding machines, which greatly improve energy efficiency, thanks to their servo characteristics that achieve high repetition accuracy.
The complexity of forming a folding machine depends on the freedom of the back gauge. In general, two backgauge movements are synchronized. High-end models can achieve a single back gauge X, Y action, allowing for good fixation and bending against beveled edges. In addition, when the workpiece is longer, the stability of the machine and the tool will greatly affect the flatness of the workpiece forming. There are several folding machines in the steel metal factory, the bending tons can be up to 320 tons, the bending length is up to 6 meters. In addition, there are models with 6-axis backgauge, which can meet the complex needs of customers.
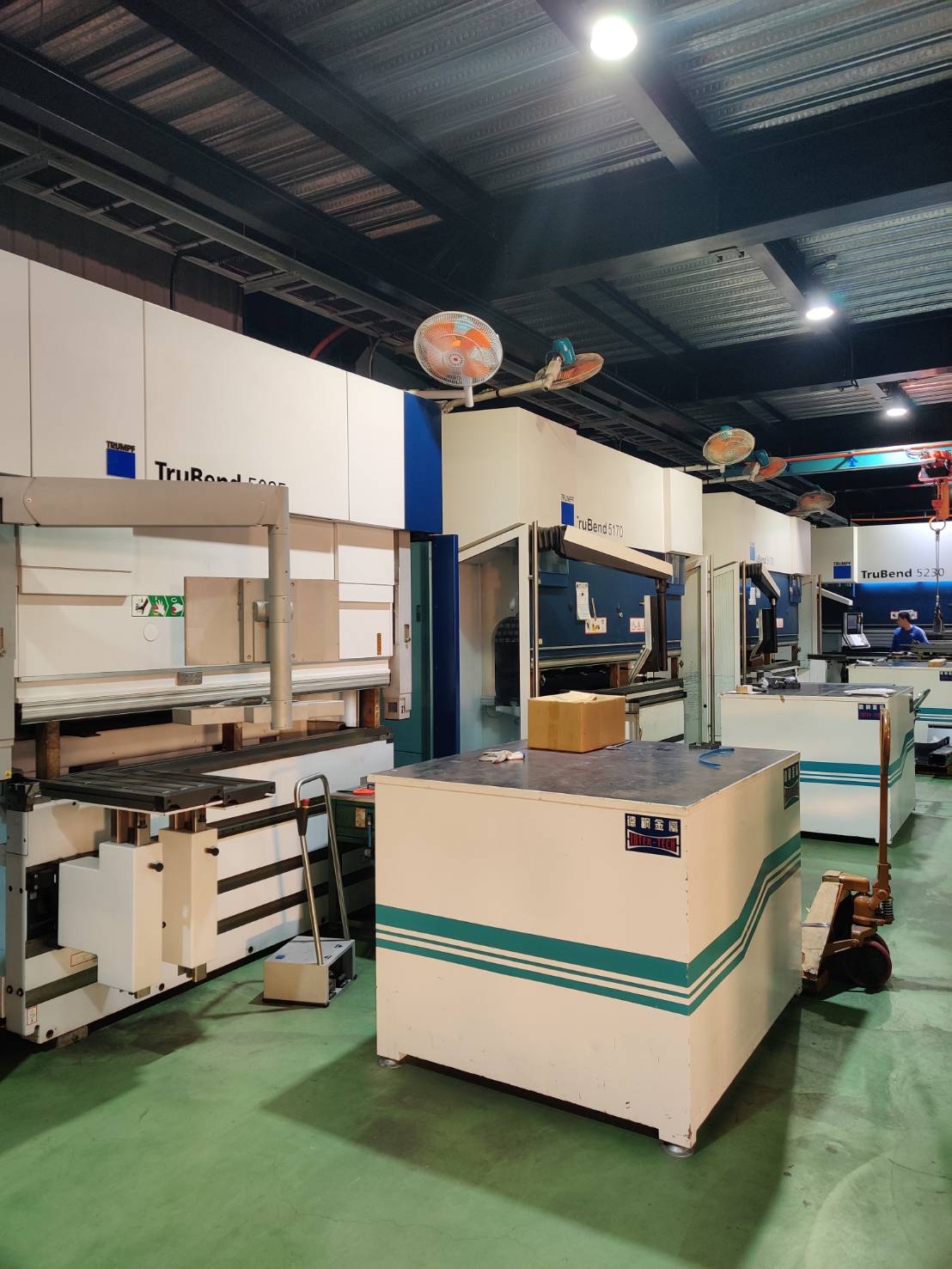
Bending Processes and Tools
The bending process involves design, bending process, and tool selection, and is a relatively complex process. Steel Metal's design team calculates the bending margin based on customer drawings and their materials, and performs prior verification with bend simulation software to avoid interference and smooth delivery over time.
For mass production, steel metal preforms the bending program in the bending software, and the automatic correction of angles with the machine can achieve high repetition accuracy. There are many types of tools in the factory, such as V-knives, U-tools, etc., and the field professional technicians will select the appropriate tool according to the requirements of the drawing. The factory's unique roller bottom mold design achieves crease-free machining quality for large workpieces.
AFTER EACH WORKPIECE BENDS, THE FIELD TECHNICIAN MEASURES THE MAIN DIMENSIONS WITH A CURSOR RULER ACCORDING TO THE DRAWING, AND A FULL INSPECTION CAN BE CARRIED OUT IF THERE ARE SPECIAL REQUIREMENTS. After confirming that the size and quality are correct, it will be sent to welding or shipped later.
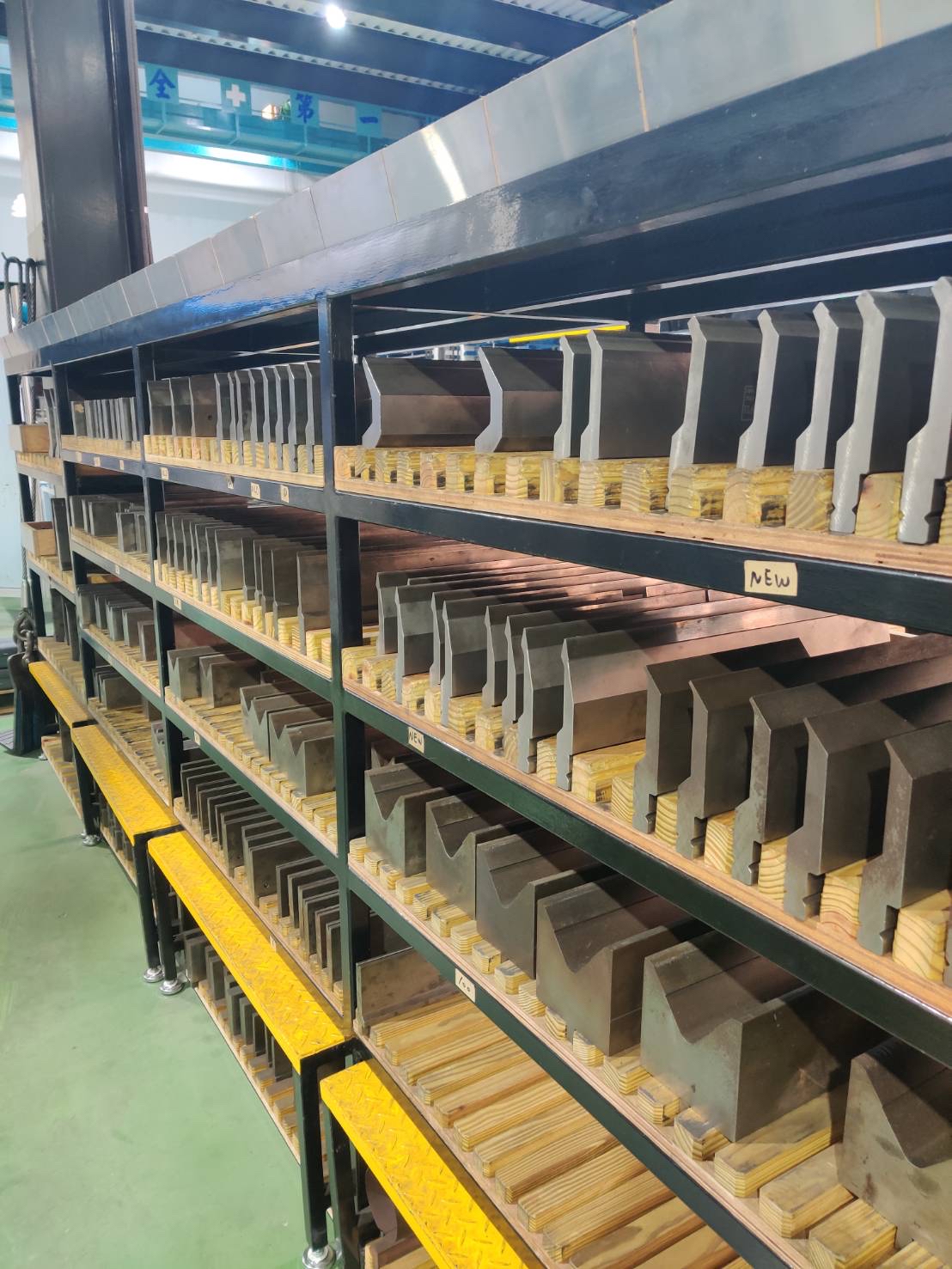
Scope of application
In recent years, TBC has achieved preliminary results in laser cutting and bending of large workpieces. It cooperates with Shin-Kok Steel to develop a C-type steel based on magnesium aluminum-zinc-nickel high-grade steel, which is now widely used in solar energy applications in fisheries and electricity.
After a highly optimized process, the 6-meter-long bending workpiece can be completed in 37 seconds (including loading and unloading), with a monthly production capacity of 1800 tons, which is highly recognized by customers and partners. In addition, in recent years, TAC has been actively positioning itself in areas such as stands for logistics equipment, medical equipment and semiconductor equipment. By passing ISO 14064-1, ISO 14067 certification, it can provide complete information on carbon emissions for the production process and transportation process, in order to meet the requirements of international carbon emissions with customers.
