Latest News & Events
Explore innovative solutions for sheet metal processing and sheet metal processing types and applications
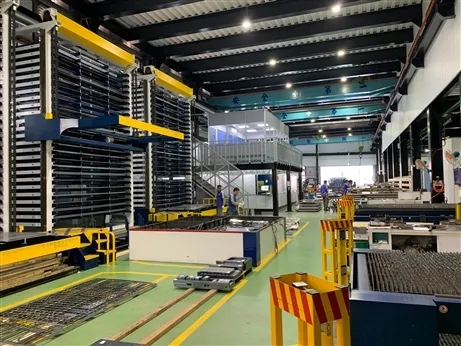
Welding and assembly stations are the final stages of sheet metal processing and are critical to the quality of finished products. When it comes to welding, it is a process that combines mainly through high-temperature melting and pressure, and relies heavily on the experience of our masters to ensure strength and stability after welding. In addition, for products that require quick joining, such as medical, logistics and other sheet metals, they can be joined by tapping nails (or rivets), but they are not suitable for highly demanding processes of dust and water resistance.
Steel Metal has decades of sheet metal design team and welders who can give welding assembly advice for different machining products. IN RECENT YEARS, STEEL HAS ALSO INTRODUCED LASER WELDING, WHICH IS HIGHLY ENERGETIC AND NOT PRONE TO HEAT, AND IS ADOPTED BY MANY HIGH-PRECISION WELDING CUSTOMERS.
Welding Assembly Process and Equipment
Common methods of sheet metal welding include
Carbon dioxide welding (CO2 welding): Carbon dioxide welding is widely used for black iron sheets because of its low cost and fast welding speed
Argon welding (TIG welding):Argon welding is suitable for stainless steel and aluminum, the welding quality is higher and the welds are beautiful
Fiber Laser Welding:Fiber laser welding uses high energy density laser beams to precisely control the heat impact zone of the weld, reducing material deformation, and is suitable for automated production with robotic arms
Mainly included in the assembly part
Nails: It is a way of permanently fixing rivets to sheet metal parts by mechanical pressure. It can be divided into aluminum studs, iron studs, stainless steel studs, high-strength studs, and so on. It is widely used for joints of thin plates.
If the customer has high requirements for the appearance of the finished sheet metal product, we will ask the welder to perform a post-weld grinding polishing to remove the solder residue and make the overall gloss uniform. Steel Metal has many years of painting partners who can help customers complete the production of the whole machine.
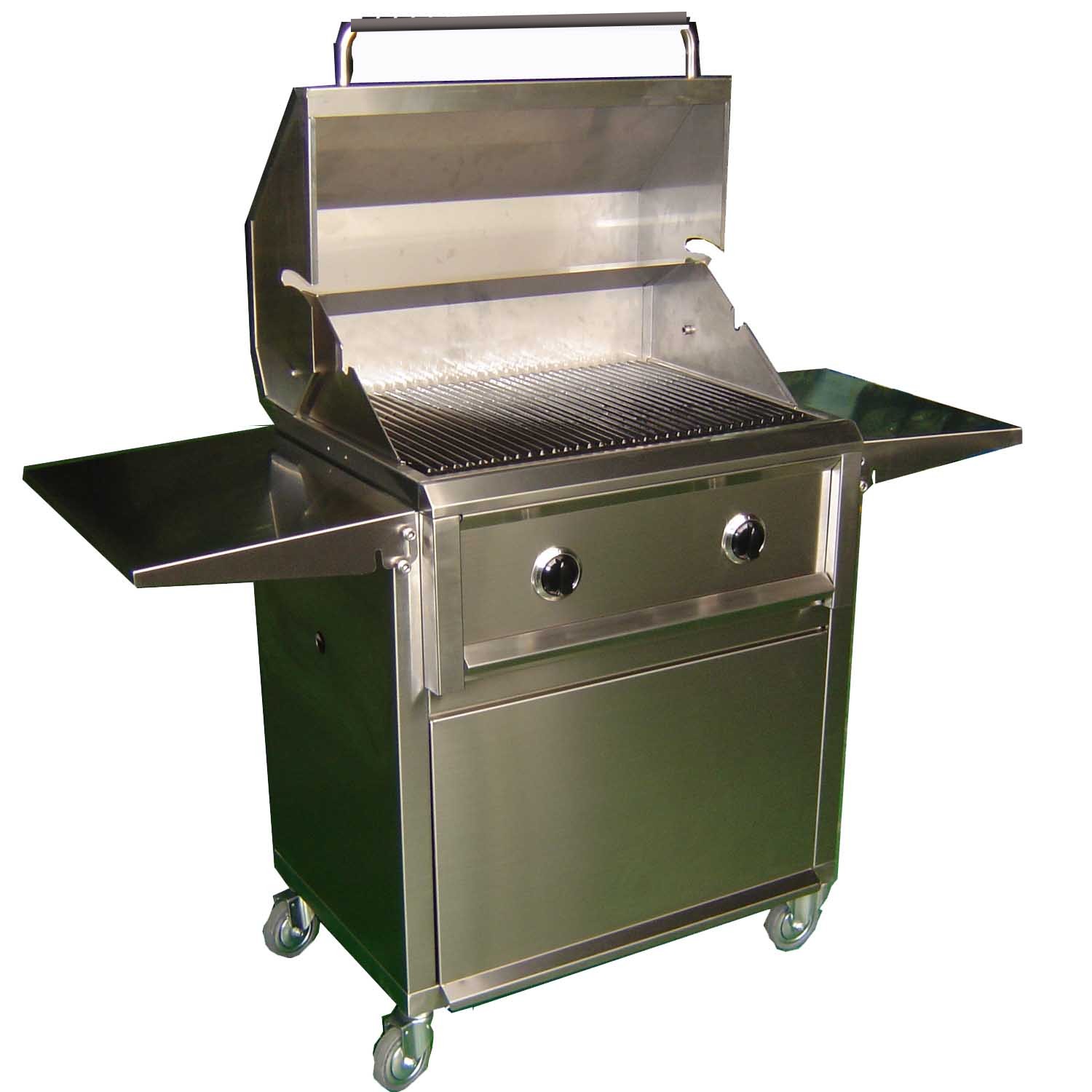
Scope of application
In recent years, the importance of semiconductors in the world and Taiwan has been reflected in the demand for many semiconductor devices. COMMON SEMICONDUCTOR EQUIPMENT PRE-INTERMEDIATE AND POST-THREE-STAGE PROCESS
Pre-process (wafer fabrication): Cleaning equipment, film deposition equipment, light etching machine, etching machine and heat annealing equipment, etc
In-process (wafer testing and cutting): Wafer testing and cutting equipment, wafer cleaning equipment, etc
Post-processing (packaging and testing): Packaging equipment, testing equipment and packaging equipment
In sheet metal processing in semiconductor equipment, even peripheral equipment (such as washing, etc.) has high requirements for processing precision and welding deformation, and the clean environment of sheet metal processing plants has its standards. Steel Metal strives to create a clean and clean production environment, and adopts high-end German IWO processing equipment, which has won the favor of many semiconductor equipment factories. Share the actual case below.
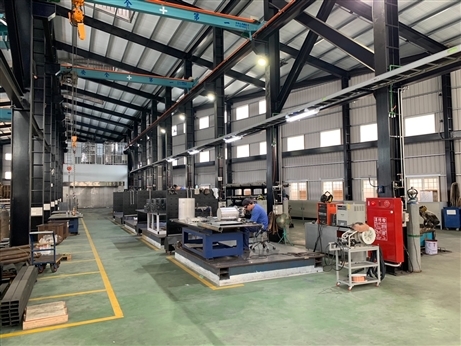