Latest News & Events
Explore innovative solutions for sheet metal processing and sheet metal processing types and applications
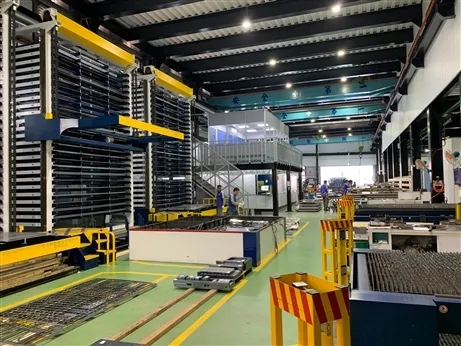
Sheet Metal Processing Concept
Sheet metal processing and sheet metal processing are easy to misunderstand, simply that sheet metal machining focuses on sheet metal (typically less than 6 mm thick) through a series of processes such as laser cutting, bending, punching and welding to produce parts or products of the desired shape and function. In contrast, sheet metal machining, or sheet metal forming, is an important stage in sheet metal processing. Sheet metal forming is used to form metal sheets using bending, stamping, stretching, etc., to achieve processes of specific shapes and sizes. Sheet metal forming is widely used in the manufacturing of automotive housings and parts. Based on the many years of processing experience at the Steel Metal Fabrication Plant, sheet metal processing is more widely discussed, so the next discussion mainly uses sheet metal processing as a substitute.
Common processing materials for sheet metal include black iron, stainless steel, aluminum and copper. These materials each have properties to suit different product needs and application scenarios.
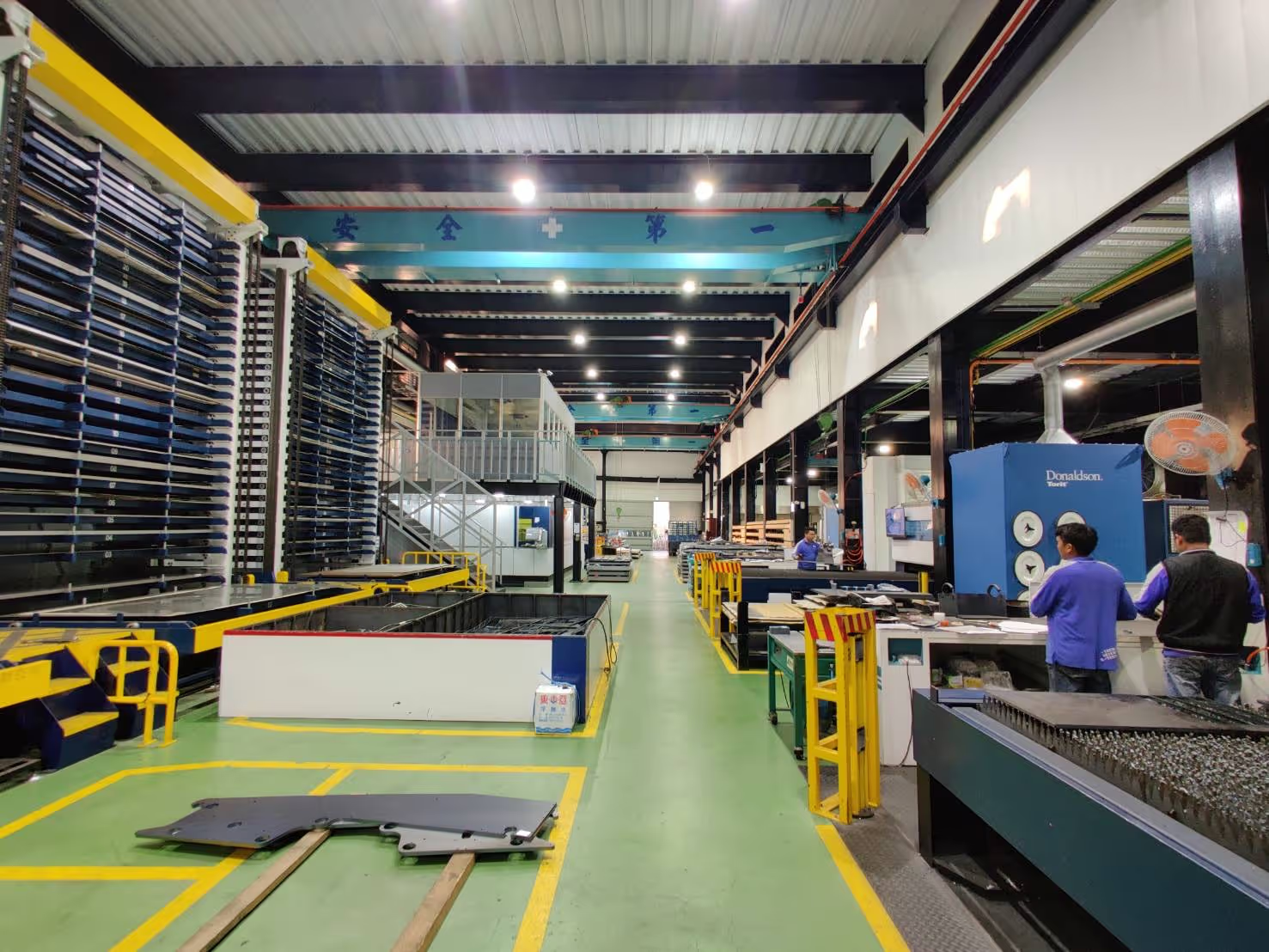
In addition, hot rolled steel (SPHC) can also be divided into low, medium, high carbon steel, etc., and low carbon steel (SS400) has a carbon content of about 0.15% to 0.25%, has good extensibility and weldability, and is widely used for sheet metal processing and welding parts, etc. (Medium and high carbon steels are used for structural elements with high strength requirements, and their low extensibility can lead to weld deformation or cracking)
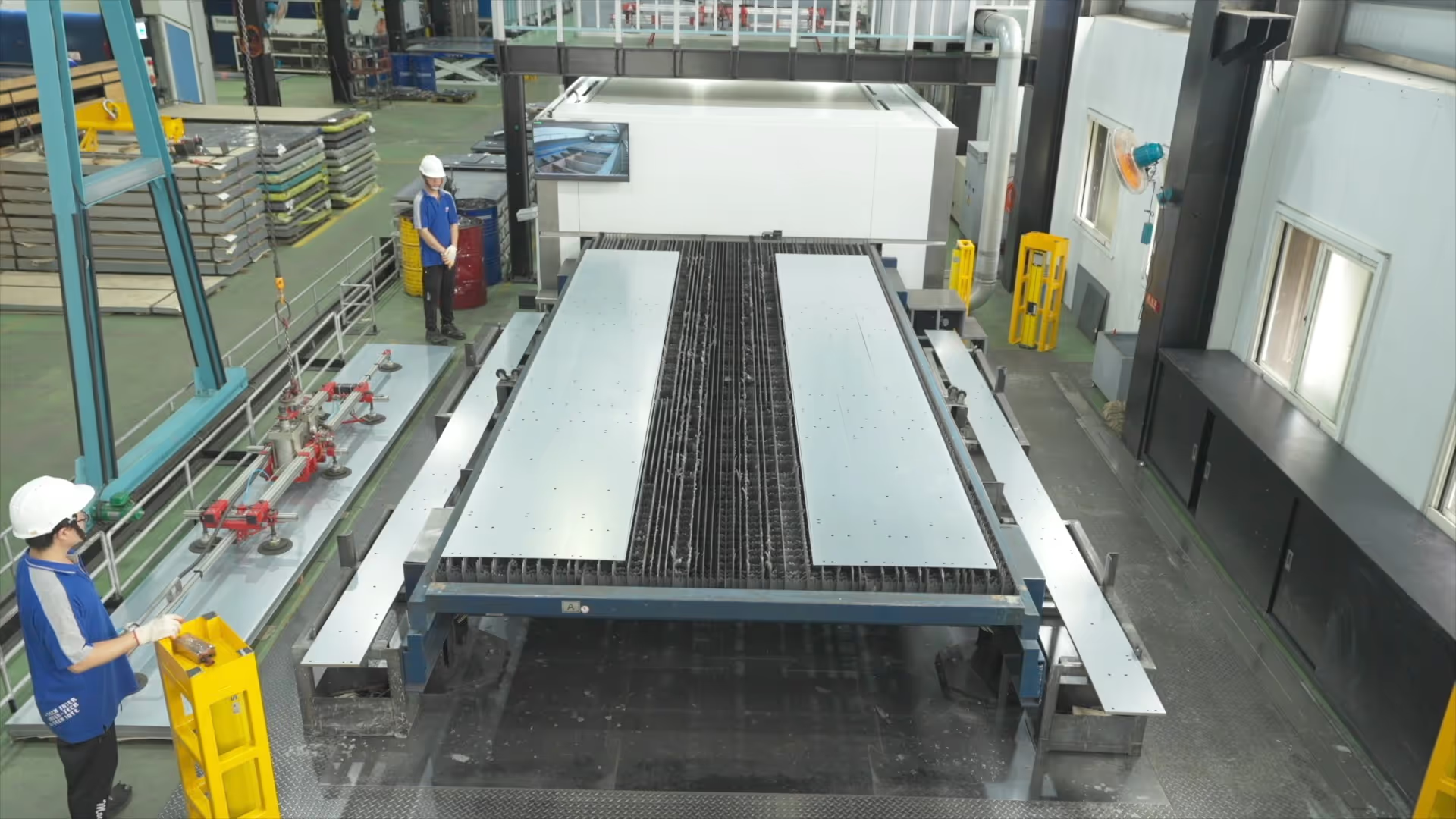
Sheet Metal Fabrication Process
The core process of sheet metal processing consists mainly of the three main steps of laser cutting, bending forming and welding assembly. In addition, post-cutting edge grinding, alignment of workpieces and coating operations are also the quality keys to sheet metal processing. The following is an introduction to the three main processes.
First, laser cutting is the use of high energy density laser beams that earlier mixed CO2 as a gas to produce laser light precision and quickly cut metal sheets into the shapes and sizes required for the design. Modern sheet metal processing multi-use fiber laser cutting machine. Its short wavelength makes metal absorption high, making it fast, cutting quality and environmentally friendly, especially suitable for stainless steel and sheet metal materials
After cutting the material, send the workpiece to the bend form. Bending is applying pressure to a flat sheet of metal through a bending machine and pressing it into a corresponding shape according to the shape of the die (e.g. V-blade, U-shaped knife, etc.). Bending requires consideration of the hardness, thickness and bending radius of the material, as well as its compatibility with the mold, etc. In addition, it is necessary to check the bending conditions at the beginning of the sheet metal design to avoid problems such as breakage.
WELDING ASSEMBLIES COMBINE MULTIPLE MACHINED SHEET METAL PARTS INTO A COMPLETE PRODUCT USING TECHNOLOGIES SUCH AS CARBON DIOXIDE WELDING, ARGON WELDING OR NOVEL FIBER LASER WELDING; HEAT DEFORMATION OCCURS DURING THE WELDING PROCESS, SO IT IS OFTEN NECESSARY TO USE CLAMPS TO SECURE THE WORKPIECE TO ENSURE WELDING ACCURACY AND PRODUCT QUALITY. In addition, rivets and bolt fasteners are also often used in the assembly of sheet metal parts.
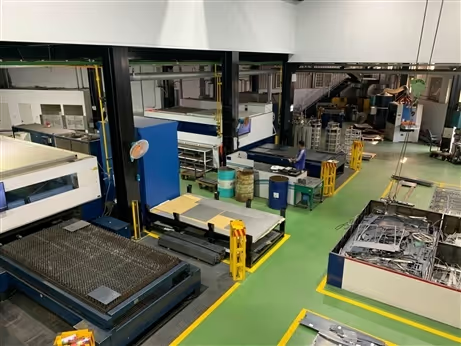
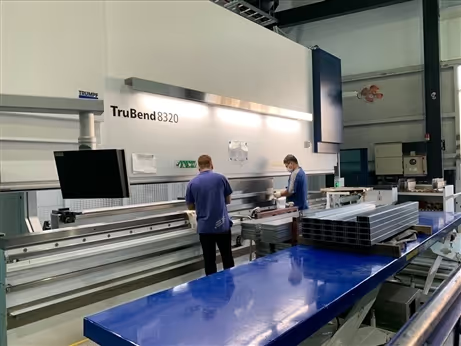
Sheet Metal Fabrication Pricing
The pricing method for sheet metal processing is usually divided into two parts of the material fee and the processing fee. If the customer provides the sheet metal (customer supply), part of the material cost can be deducted. For example, Ethical Steel can be discussed according to customer requirements.
Material FeesCalculated mainly according to the actual typesetting results and the type of sheet material used, the thickness and the actual consumed weight includes the actual working weight and the remaining waste. The typesetting department will also provide the typesetting style for the customer to confirm after the typesetting process to ensure that the scrap meets customer expectations. In general, waste is around 5-20%, depending on the shape of the workpiece being cut.
Processing FeeIt covers laser cutting, bending, welding, etc. Laser cutting costs are priced according to the length of the cutting path. The unit price will vary depending on the material type, thickness and hole size, etc. Bending processing costs are usually calculated based on the number of bends, and for large or long workpieces, there is also a pricing pattern. Welding costs are estimated based on the length of the weld or the number of weld points, multiplied by the welding time or the weld length.
Steel Metal is a long-term relationship with customers, so design and processing advice can be given according to cost requirements, ensuring that the quality and cost of finished products meet expectations.
Sheet Metal Fabrication Applications
Sheet metal processing is widely used in various fields, such as mechanical equipment, kitchen equipment, medical equipment, etc. You can even see the representation of sheet metal processing and design in the installation arts, and so on. We can say that sheet metal processing is related to our 4 lifetimes. The following is an overview of the main areas and applications of steel metal.
Machinery
Sheet metal processing is mainly used in the manufacture of mechanical housings, control boxes, cabinet enclosures, brackets and transmission components, etc. These parts require robust construction, high dimensional accuracy and effective protection of internal mechanical components from external environmental influences. Common materials include cold rolled steel plate (SPCC) and stainless steel (SUS304)
Logistics Industry
For logistics equipment such as shelves, transport vehicles, storage boxes, etc., sheet metal processing focuses on durability and lightweight design for easy handling and stacking. The machining process requires the ability to handle large machining and batch production, and the introduction of the 6-meter Bending Machine by Deutsche Steel in Germany can quickly meet this demand.
Medical Equipment
Sheet metal parts for medical equipment require extremely high precision and surface cleanliness. Stainless steel or special alloys are often used to meet hygiene standards and corrosion resistance requirements. Due to the stringent requirements for the machining process, plant cleanliness and process professionalism are key indicators that determine quality.
SEMICONDUCTOR EQUIPMENT
THE SEMICONDUCTOR INDUSTRY DEMANDS HIGH PRECISION OF SHEET METAL PROCESSING. THE PARTS ARE MOSTLY USED FOR CHASSIS, FRAMES AND CLEANROOM ACCESSORIES OF PROCESS EQUIPMENT. The material is usually chosen with high quality stainless steel (such as SUS316) or aluminum alloys, emphasizing cleanliness, corrosion resistance and good mechanical performance. ALL STEEL METAL FACTORIES USE GERMAN HIGH-END LASER CUTTING AND FOLDING MACHINES IN ORDER TO PROVIDE CUSTOMERS WITH THE BEST QUALITY AND DELIVERY TIME.
Energy industry
In recent years, DEK Steel has partnered with domestic listed companies to produce solar brackets, replacing the previous extrusion molding process through special crimping processes. This approach is in line with the expectation of mass production and customization of workpieces. Currently, the solar brackets that coexist in many parts of the country are supplied with steel metal.
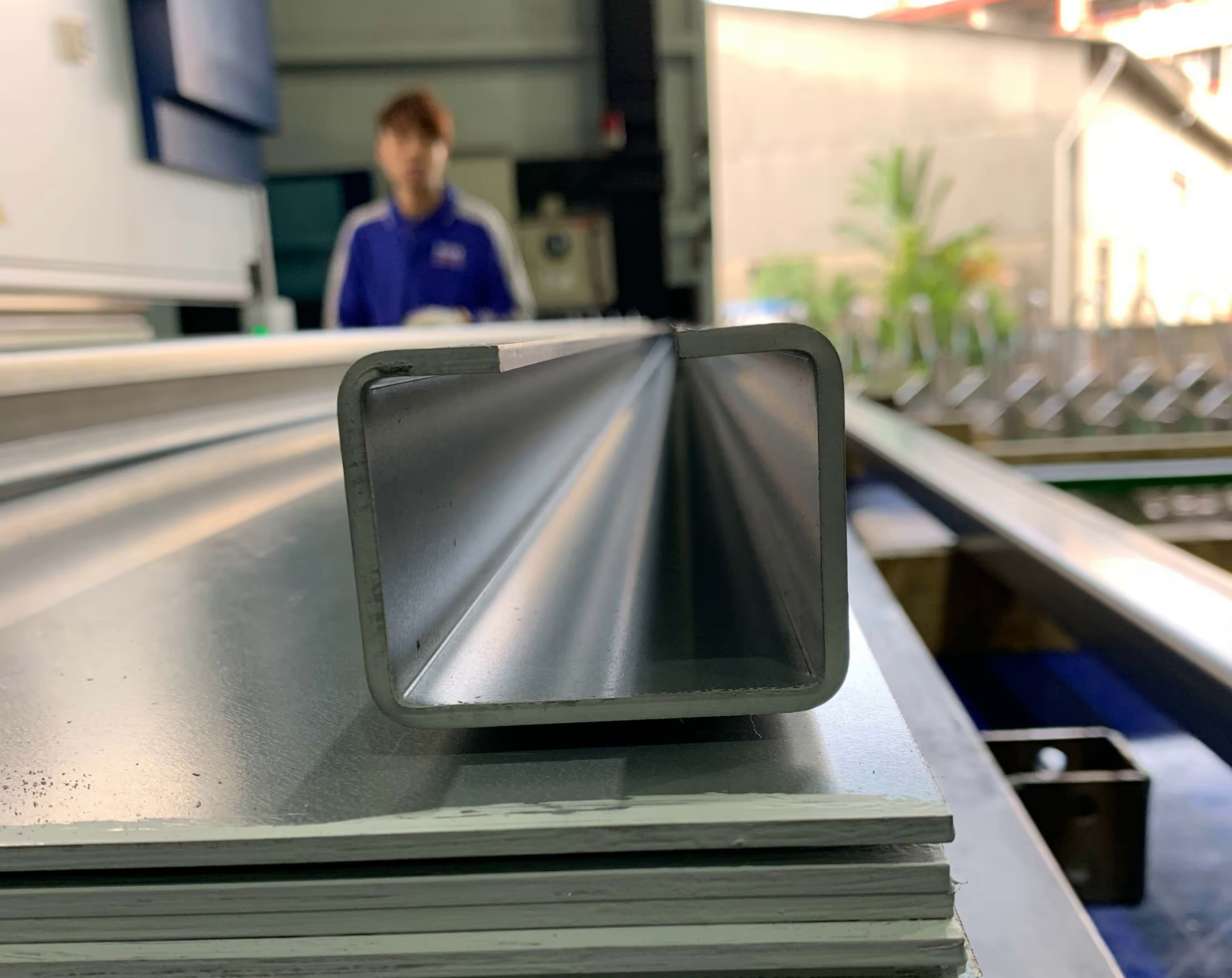
The Future of Sheet Metal Fabrication
In recent years, due to international upheavals such as the Sino-American conflict, the war in Russia, and the gradual dismantling of the formerly globalized supply chain, major factories have begun to adopt a short supply chain strategy to deal with change by closely connecting with suppliers.
Steel Metal has been actively promoting digitalization with ISO 14064-1, ISO 14067 carbon reduction certification since 2020. The digitalization aspect is the introduction of the production management system in Germany, which allows you to quickly control the movement of each customer order, machine harvest rate, stock sheet water level, etc., and transparent control of production to guarantee the delivery of each batch.
ISO 14064-1 focuses on monitoring and reporting of greenhouse gas (GHG) emissions at the organization level, while ISO 14067 focuses on the Carbon Footprint of Products (CFP) at the product level. These two certifications have become mandatory for metalworkers due to EU regulations such as the requirements for carbon emissions from products. TAK METALS IS THE FIRST IN TAIWAN TO PARTNER WITH KPMG THROUGH TWO MAJOR CERTIFIED SHEET METAL PROCESSING PLANTS TO PROVIDE COMPLETE CARBON FOOTPRINT REPORTS FOR EITHER INTERMEDIATE OR MASS-PRODUCED PRODUCTS, HELPING CUSTOMERS TO HAVE COMPLETE CARBON FOOTPRINT DATA FROM THE SOURCE.
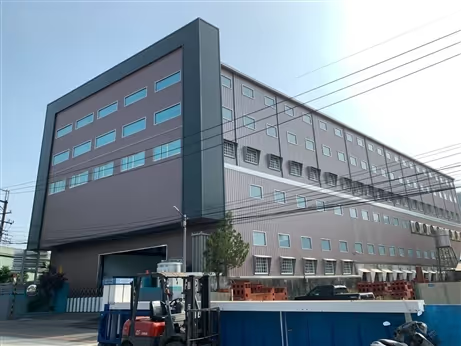