Latest News & Events
Explore innovative solutions for sheet metal processing and sheet metal processing types and applications
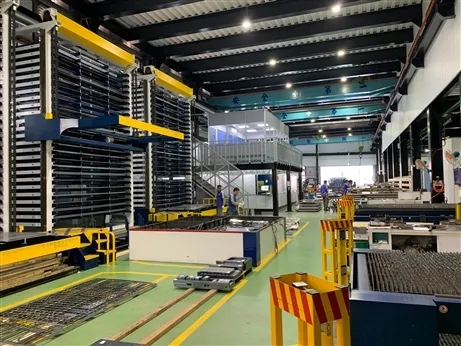
Laser cutting is a high-energy precision machining technique whose core principle is to focus the laser beam on the material surface, causing the local area to instantly rise to a molten or vaporization state, and to form a precise incision through the blowing of the molten substance by assisting gases. The whole process is driven by a computer numerical control (CNC) system. After typing software enters the design drawing file, the machine automatically calculates paths and parameters for high precision cutting.
In terms of sheet metal processing, laser cutting can be divided into two modes:
Melting Cutting:Blown molten metals with inert gases (such as nitrogen). Suitable for stainless steel and aluminum alloys, the cut is non-oxidized and the surface is smooth.
Oxide Cutting: It uses oxygen and metal to heat release to improve cutting efficiency, but may produce oxide layers, mostly used in carbon steels.
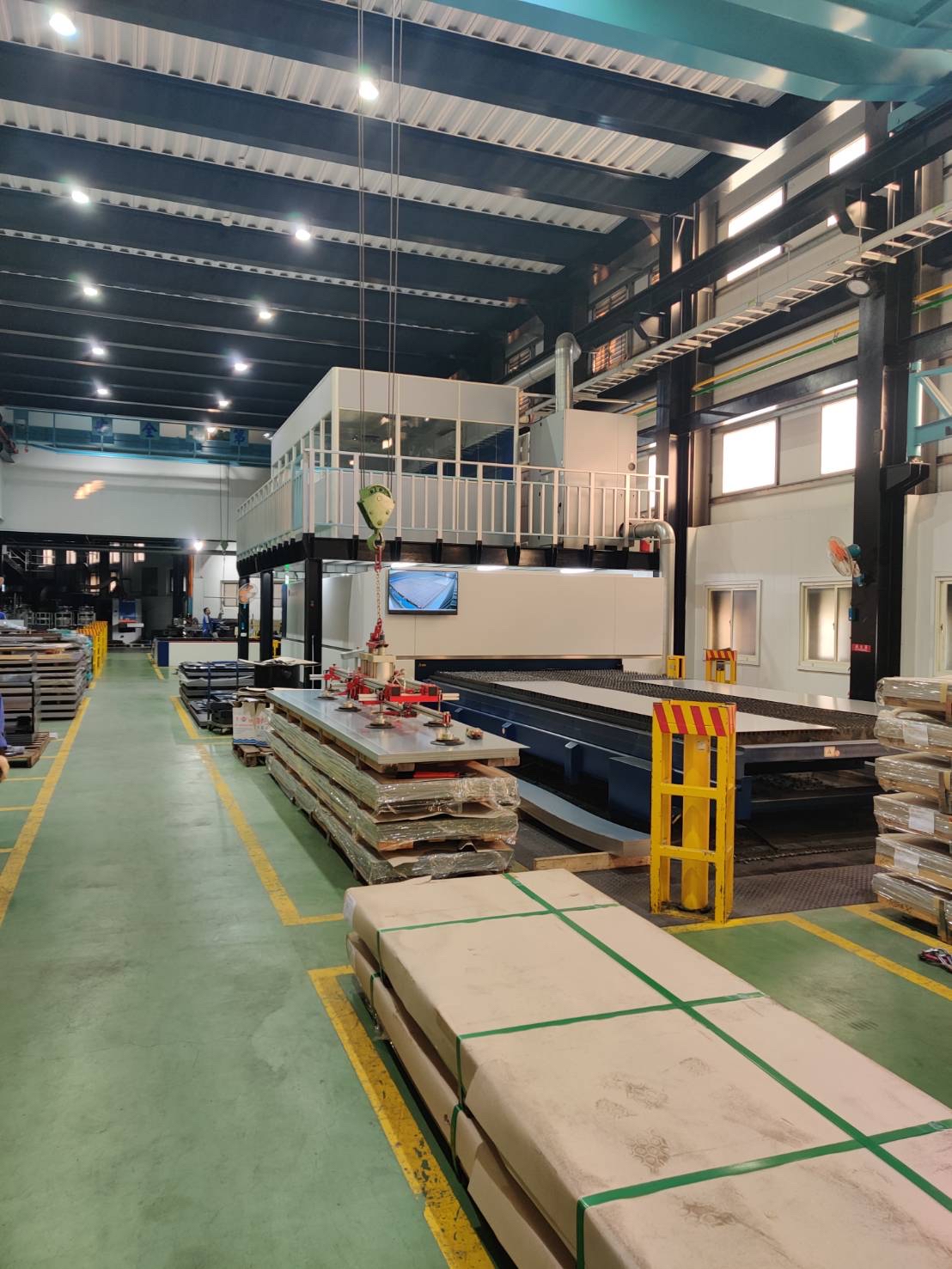
Common laser cutting for sheet metal processing includes the following two types
Fiber laser
Fiber laser cutting machine can produce very high power and is suitable for cutting almost all materials such as metals, alloys, non-metals such as wood, glass and plastic. Because of its high energy conversion efficiency, the cutting efficiency is much higher than traditional CO2 lasers.
The steel plant has four German TrumpF (TRUMPF) laser cutting machines that can cut up to 6m workpieces, 60mm carbon steel, 60mm stainless steel, and 40mm aluminium, for Taiwan's few independent sheet metal plants that have the capacity to produce large workpieces.
CO2 Laser
CO2 laser is the most common form of laser, because of its high efficiency, good cost effectiveness, and can cut a wide variety of materials at high speed, and is widely applied to the cutting of sheet metal (<6mm). CO2 lasers have lower cutting efficiency than mainstream fiber lasers, with longer cutting times and high power consumption. Due to the trend of energy saving and decarbonization, Steel has completely replaced CO2 lasers with fiber laser machines.
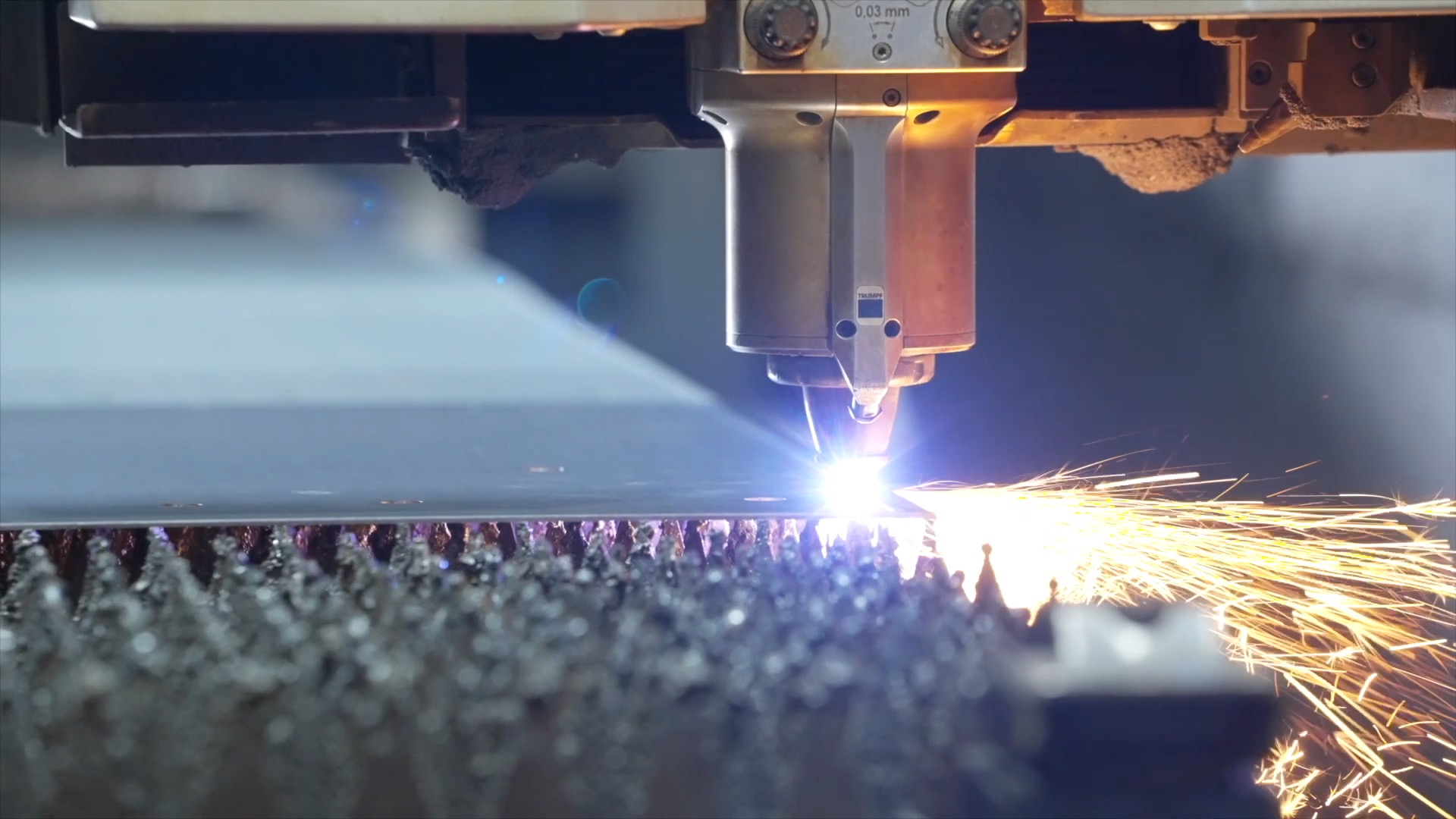
Laser Cutting Process
The workflow of laser cutting can be divided into loading, cutting and discharging (receiving), and each step depends on the quality of the cut finished product.
Top Preparation
Feed the corresponding plates, such as black iron plate, stainless steel plate, etc. (up to 3mx1.5m) to the exchange table; At this time, the CNC receiving typesetting unit is sent to the cutting path of the machine. The professional can start the cutting operation after confirming the accuracy of the cutting point, interference, etc.
Cutting is carried out
The laser cutting head cuts according to the path and parameters. In general, the design team and the typesetting team can simulate it on a computer to ensure the stability of the overall cut. However, for complex contours or special quality requirements (such as R angle), secondary training is required by an on-site professional.
Substrate and Receive
After cutting, the finished product and frame need to be separated. This part relies heavily on factory management to ensure that the separation and receipt workpieces are placed in the correct position and shipped to the proper process.
For steel metals, all of the above processes can be controlled through a digital production management system, and through carbon offsetting database matching, customers can gain full control over the carbon footprint of each batch of materials.
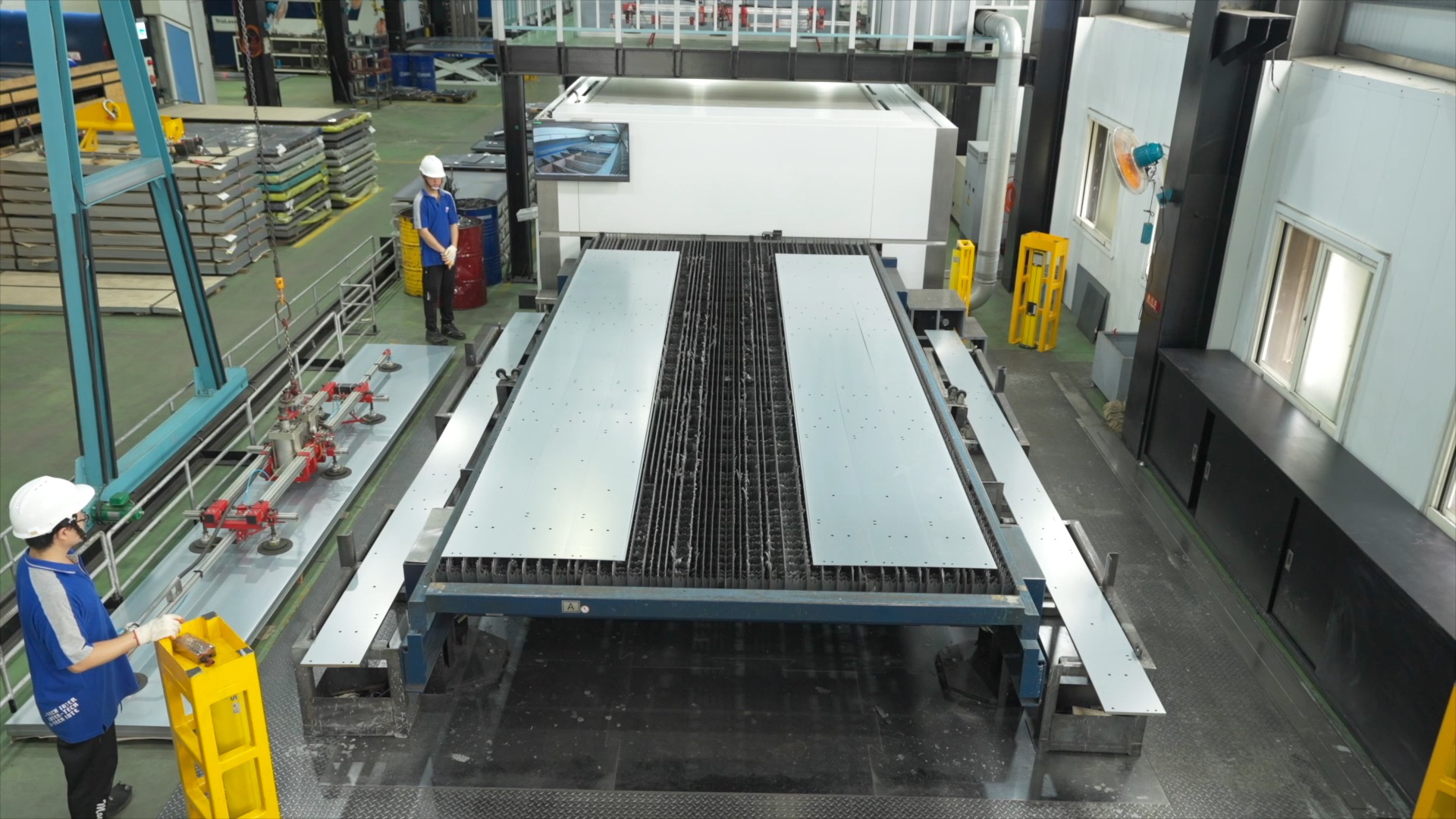
Scope and Future
The popularization and high efficiency of fiber laser cutting has been gradually moving towards automation and thick-plate cutting. In terms of thick plate cutting, Steel Metal is the first laser cutting machine in Taiwan to have a 24000w German Impulse laser cutting machine. The cutting performance can reach 60mm carbon steel, 60mm stainless steel, 40mm aluminum plate, which can replace water knife or flame cutting, while maintaining the overall quality of the workpiece under thick plate cutting.
In addition, due to the fermentation of carbon emissions issues, the metalworking industry is the first to take a hit. Fiber laser cutting has a high conversion efficiency and significantly saves energy consumption, saving about 50% compared to CO2 lasers. In addition, the combination of professional typesetting with the characteristics of fiber laser small gaps (Kerf) can significantly reduce waste after cutting. Steel Metals has a complete carbon footprint database for energy use and materials for cutting, etc., to generate carbon footprint reports for workpieces produced for customer needs.